AFM-in-SEM method for failure analysis of bipolar junction transistors (BJTs)
Performing a professional failure analysis
Benefits of fault analysis with LiteScope
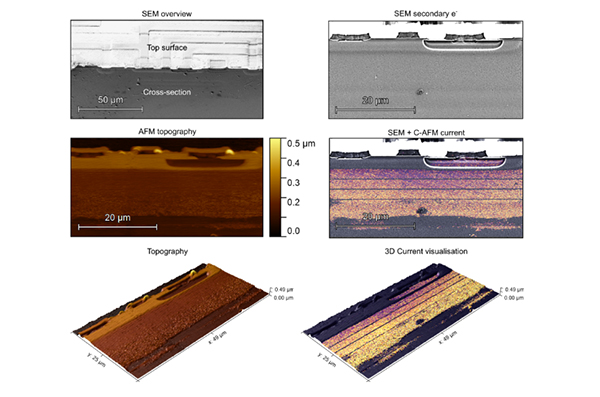
Image: Cross-section of a Bipolar Junction Transistor (BJT) - Analysis after FIB etching
Sample courtesy of David Pléha, ON Semiconductor
BJT's and their weak points
Semiconductors are the backbone of modern electronic devices and systems. Bipolar transistors, especially bipolar junction transistors, have proven to be indispensable components in this context.
However, anyone involved in the manufacture, design, or application of BJTs knows that they are not infallible. Manufacturing errors, material defects, design problems and environmental influences can cause a transistor to not perform as expected or to fail prematurely. This is where failure analysis comes in.
Failure analysis is a critical process for understanding the causes of bipolar transistor malfunction or failure.
Extend the 2D SEM image to 3D and thus improve the material contrast in the SEM.
What are the benefits of performing a professional failure analysis?
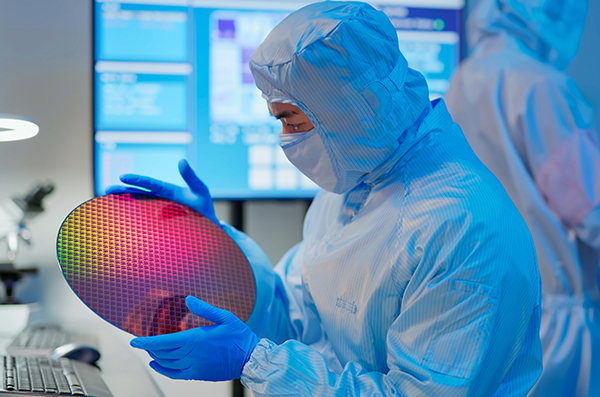